GUZ BOX design + audio

Processed with:
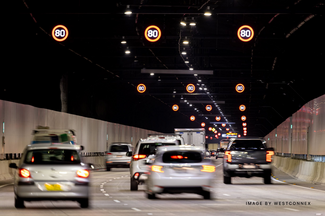
Introduction & Project Overview
Located in Sydney NSW, Australia, WestConnex is the world’s longest road tunnel infrastructure. It was designed to ease traffic congestion and connect communities across Sydney. WestConnex took 7 years to plan and build and was completed in November 2023, providing motorists with a continuous 33 km traffic-light free motorway network. The network includes multiple tunnels, each of several kilometers long, with one to five lanes, transitions, merge and break-down lanes.
The sound system to be designed was part of an overarching life-safety concept and was to be used in warning and evacuation scenarios in the tunnels themselves, as well as to cover cross passages between the tunnels and long egress passages.
Challenge
For the announcement system, the requirements were initially given as follows: speech intelligibility at an average STI of 0.48, minimum signal-to-noise ratio of 10 dB, and maximum SPL of 105 dB (A) at an assumed ambient noise level of NR85. That may sound doable at first, but a few following factors that are relevant for any road tunnel like this make the goal extremely hard to achieve.
First is the tube-like shape of the tunnel and almost all the surface materials based strictly on concrete, due to the fire-resistance and long-durability requirements. Geometrical specifications were completely fixed in both respects, dimensions as well as acoustic materials, so that no changes could be made by the acoustic consultant in order to improve the room acoustic parameters of the space. The focus therefore had to be put on the electro-acoustic design, especially the horn sound system design and software-based acoustic simulation and optimization.
Second, the required SPL of 105 dB (A) proved to be too high for this space due to the masking effect in play, so that perceptually the audio content was too loud to be heard clearly. The subjectively realistic SPL was found to be about 95 dB (A), leaving very little headroom for the noise floor to be 10 dB away. In fact, noise measurements showed LAeq levels of up to 90 dB (A) due to the massive jet fans for tunnel ventilation and also possibly active deluge systems. In practice, there was simply no room to increase the loudspeaker gain and signal-to-noise ratio.
The third is the acoustic model itself. The challenge of making a working acoustic model for long tunnels is to break it down into shorter segments, while making sure none of the simplifications compromise the accuracy of the simulation. In particular, that in the broken-down model, the acoustic influence of the neighbor segment is negligible to the section under research.
Project Execution & Results
The work demanded a detailed survey of the acoustic conditions and a series of on-site acoustic measurements in this and similar tunnels, including obtaining initial impulse response data, noise levels in various scenarios, and reverberation times using large balloon bursts. The latter was required as it could provide up to 128 SPL at 10 m (unlike a regular dodecahedron) within a frequency range down to 50 Hz. In addition, environmental parameters such as air temperature and humidity obviously play a role in a reverberant room over long distances, and were measured and accounted for accordingly.
However, the most time-consuming part of the project was building the working acoustic model, dividing the entire tunnel into typical segments and running a series of simulations for each. Obviously, segmentation simplifies the management of the computer model and reduces the computational time required. Dealing with such large models is hard work in itself, but to obtain valid acoustic results, the engineer also has to find the minimum segment length where the influence of neighboring segments is acoustically negligible. The segment lengths of 1 to 2 km were calculated based on two criteria:
- Minimum segment length by absorption: The area of the ends which are each modeled by a fully absorptive surface is less than 1% of the total segment surface area and less than 10% of the total absorption area. This means a negligible effect on both RT and STI.
- Minimum segment length by loudspeakers: All loudspeakers outside of the modeled segment would increase the total received level by no more than 1 dB, resulting in a negligible effect on STI.
Built in AutoCAD and imported into the EASE acoustic simulation software, each segment was calibrated to a combination of reverberation time and impulse response measurements. Some of these measurements were made in already existing tunnels with comparable acoustic conditions. The absorption and scattering characteristics of the surfaces were partly modeled using AFMG SoundFlow and AFMG Reflex software.
Finally, to achieve the best possible design results, the loudspeaker positions were determined to be at 40 m intervals and positioned as close as possible to the potential receivers, just above the vehicle clearance height. For the primary loudspeaker model, a large horn of approximately 1.2 m in size and narrow directivity was defined and custom-built for the project.
The simulation also confirmed the solution to align all the speakers in the tunnel in time with the first speaker at one end of the tunnel. In this way, a sound wave generated at one end and traveling down the tunnel was continuously reinforced by successive lines of speakers. Delays and pointing angles were also fine-tuned according to the shape or curve of the segment, and later confirmed on site. Depending on the width of the tunnel and the number of lanes, one to three loudspeakers were defined for each cross-section. Finally, the output levels were adjusted for maximum signal-to-noise ratio, high-passed to improve signal transmission for the speech bands, and all of the above solutions were optimized for the highest speech intelligibility (STI).
This extensive engineering work of many iterations was possible to handle within the EASE simulation suite.
During the project execution a few interesting outcomes were found. For instance, the project’s design specification called for signal levels at 10 dB above ambient noise levels, as stated above. However, in practice, it was found that the highest STI is achieved at signal levels of about 95 dB(A) translating to an SNR of just 5 to 6 dB. Subjective evaluation on-site confirmed these findings. That means that the EASE software simulation, above all, can conveniently find and prove better solutions outside of the initial requirements range.
The final commissioning and STI validation measurements showed good consistency across tunnel segments and matched predicted values within typical uncertainties. Both the required average STI of 0.48 with jet fans off, and the desired STI of 0.45 with jet fans on were successfully achieved.
Big thanks to Tim Kuschel, the acoustic consultant engaged by the audio systems integrator for the WestConnex project and AFMG’s official partner in the South-East Asia region, for sharing the data with us. Also big thanks to Michael Fitzgibbon from CNG Systems for assistance in gathering and verifying the acoustic data. Special thanks go to Peter J. Patrick who inspired parts of this discussion and established some of the foundations with his preceding work.
Check out the full list of the outcomes and many more about the project in the paper presented at AES 2024 in New York: Acoustic modeling and designing of emergency sound systems in road tunnels.